Cooler installation
1. Pay attention to the relevant safety measures during installation, and ensure that there is no installation stress during the installation operation. To reduce tension and cushion vibration, use flexible connection elements and shock-proof gaskets. To install the nozzle, filter and sleeve, hold the connected part with a wrench to avoid damaging the cooler. The connection between the inlet and outlet pipes and the cooler must be stress-free and vibration resistant. Do not allow the cooler to bear or support other parts of considerable weight. Special care should be taken not to damage sealing surfaces, flanges and joints during installation.
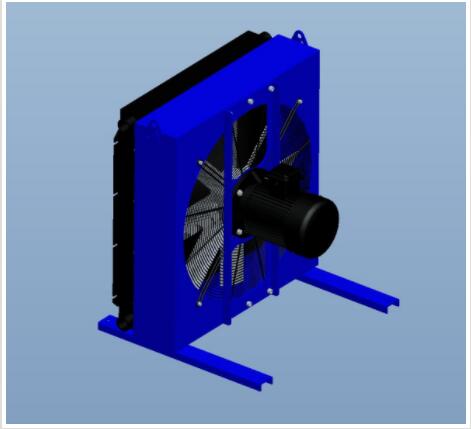
⒉ Oil medium at low temperature, viscosity increases, so low temperature start, may produce more than the allowed range of peak pressure: or in the instantaneous large flow, will also produce more than the allowed range of peak pressure. Therefore, a bypass valve must be installed to protect the cooler.
3. In the hydraulic system and lubrication system, there are often pressure peaks, which may reach several times the maximum pressure. These peaks appear in the form of pulses, which can only be recorded by oscilloscope. Due to such a short peak time, the normal overload valve can not respond in time, which is far from enough to eliminate the pressure shock and pressure shock in the system. In such cases, safety and reliability concerns recommend the use of a separate circulating cooler loop.